For a lathe, its cutting function depends on its surface roughness, resulting in different cutting speeds and feed speeds. High-precision grinders have very high requirements for parts. Lathes with higher precision require higher complexity, and whether it is a plane or a curve, it only needs to be A straight line may be required to divide between two points. So, what is the development trend of high-precision grinding machines?
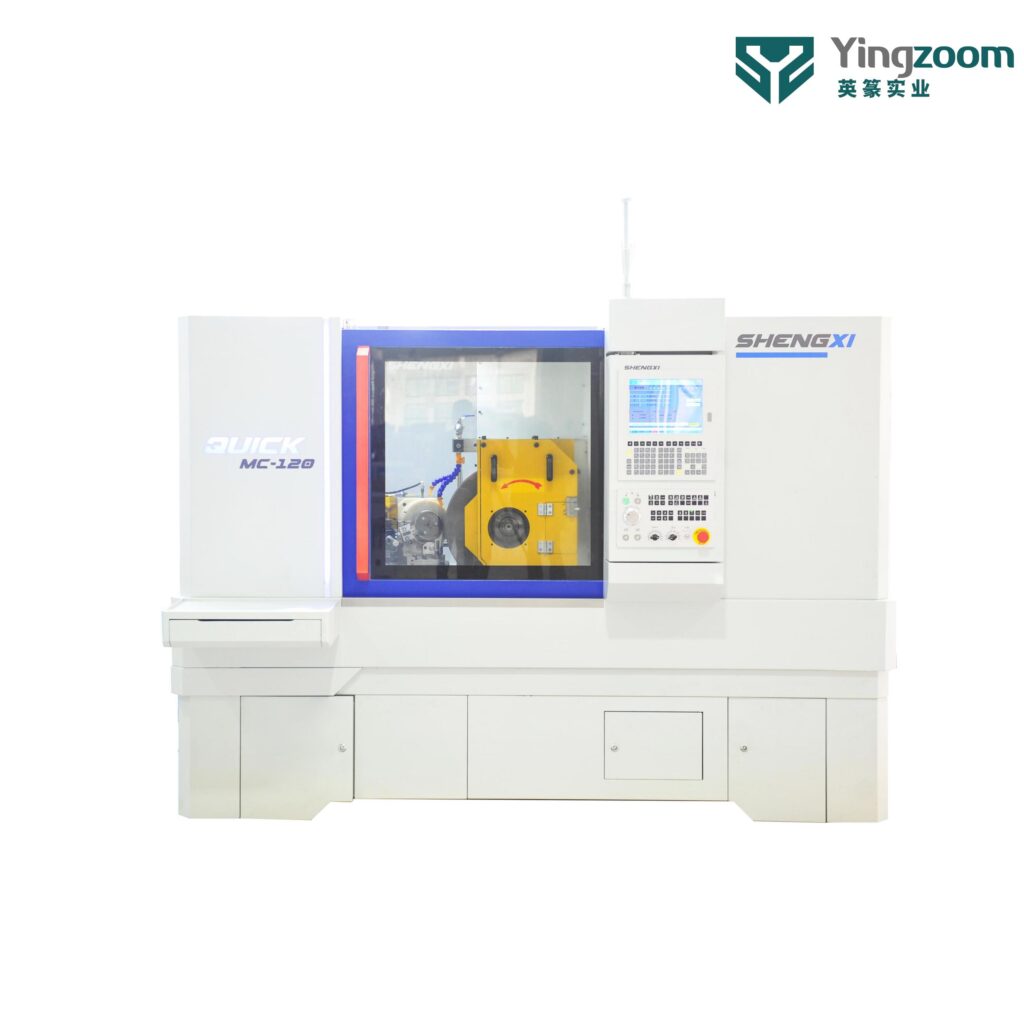
1.Develop towards intelligence and flexibility
Combining CNC technology, neural network, automatic clamping, real-time monitoring, online inspection and CAD/CAM and other advanced technologies, we use intelligent and flexible control methods to process and process complex, precise, small batches or even several pieces quickly. Problems in micro-grinding of many types of tiny parts. The application scope of micro-grinding technology is constantly expanding, including various engineering materials such as titanium alloys, aluminum alloys, steels, glass, cemented carbide, etc., ceramics and other non-metallic materials and various composite materials.
2.Development towards composite processing technology
Vigorously develop composite processing technology that combines micro-grinding technology, such as laser, EDM, electrochemistry, ultrasonic vibration and other technologies to meet the needs of high-precision parts and the processing of constantly developing new materials. requirements, while effectively improving processing efficiency and processing quality.
3.Develop towards high precision and efficiency
Choose a high-precision grinder with good service. In order to meet the requirements of the increasing diversification of materials for ultra-precision micro parts, the gradual specialization of structures, the continuous high-precision of dimensions, and actual production needs, micro-grinding technology must move to the nanoscale. The development of high precision and high efficiency at the analog macro scale requires vigorous development of high-performance micro-grinding machines, especially key components such as ultra-high-speed ultra-precision micro spindles and fast-feed ultra-precision micro worktables.
Utilize the connection between accessories for grinding to achieve high precision. After processing and running-in of parts, high-quality products are created. High-precision grinders have good quality and a good reputation. There is a floating amount between the required and specific assembly, but A good equipment, no matter what type, range, structural features, etc. can achieve customer satisfaction through processing.