A good machine tool is inseparable from a good casting, and a good casting is naturally inseparable from the properties of the material and the long-lasting experience of the workers. High-precision grinders require sufficient strength of the casting itself, low stress, and good cutting and material stability. Inferior castings will lead to poor results. So, what is the process of multi-objective optimization of high-precision grinder bed?
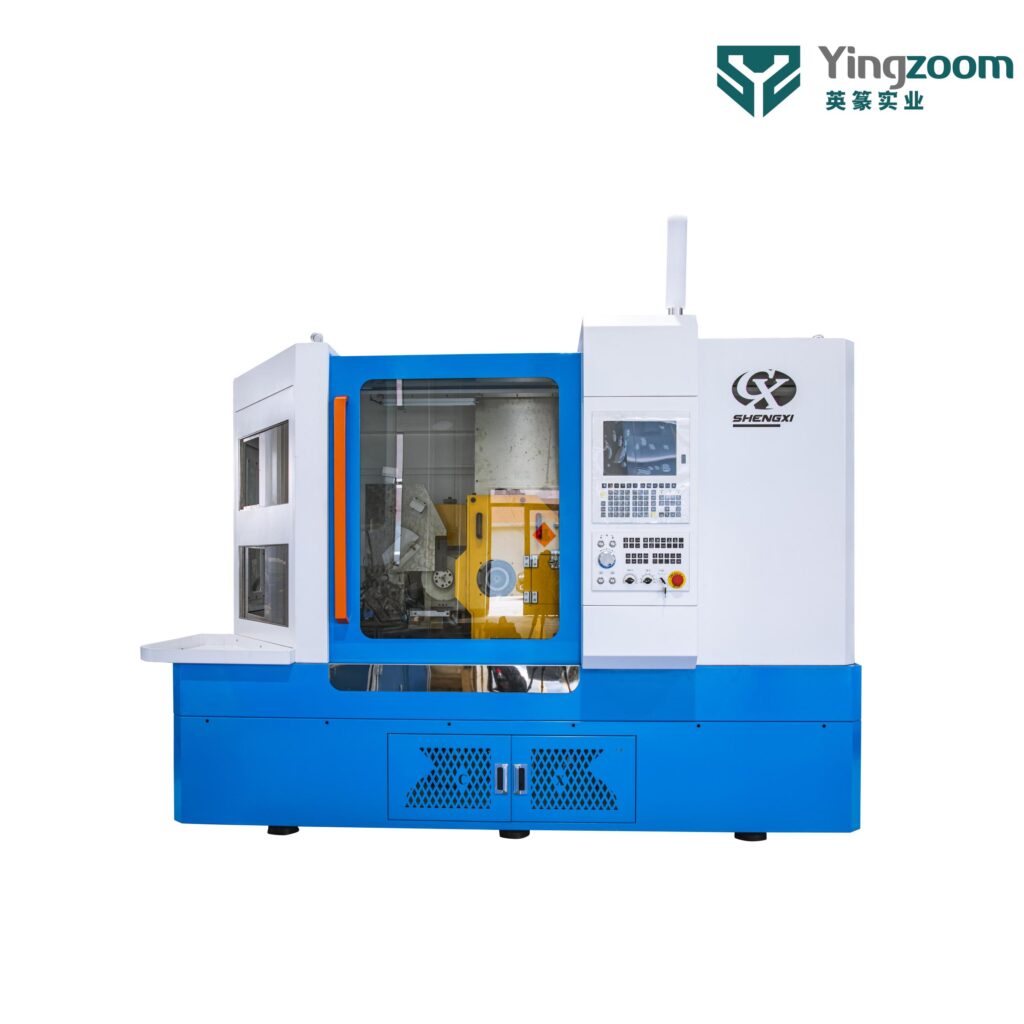
1.Establish corresponding multi-objective optimization mathematical model
A high-precision grinder with good service and strong strength uses the parameters such as rib thickness and position size that have been imported into the software as variables, takes the static deformation of the grinder bed as a constraint, and takes the overall quality of the bed and the first-order natural frequency as the optimization goal. Create a multi-objective optimization model in the software module. Set the value range of each parameter, the initial value of the parameter and the analysis range according to the actual situation. Based on the multi-objective optimization module, the first-order natural frequency of the grinder bed and the overall mass of the bed are used as the optimization objective function, and its static deformation is used as the constraint condition. The parameters as variables are set, their value ranges are determined, and the corresponding multi-objective parameters are established. Objective optimization mathematical model.
2.Obtain the sensitivity of the objective function
After selecting a good high-precision grinder for optimization analysis, the system will generate a corresponding number of samples according to the number set by the user and solve them. Then it will calculate three sets of multi-objective optimization solution sets based on the optimization goals, and also obtain each variable ( parameters) to the constraints and the sensitivity of each objective function.
3.Multi-objective optimization
The sensitivity of each variable to the overall mass of the bed. It can be seen that the overall mass of the bed will increase as the thickness of the ribs increases; they are the sensitivity of each variable to static deformation and first-order natural frequency; and the effects of the dimensions of the front bed ribs on the results The impact is not significant, mainly because the static deformation is located at the rear part of the rear bed, and the first-order vibration shape is also the upper part of the rear bed swinging laterally. Therefore, in order to achieve structural optimization, in addition to optimizing the size of the ribs, the rear part of the grinder can also be optimized. The bed structure is optimized accordingly, with the aim of improving its first-order natural frequency.
High-precision grinding machines are more difficult due to the reliable quality they require. This requires the executors to have high expectations for their castings, not to be impatient if they do not proceed, but to wait quietly and patiently, and to be a little paranoid about their grasp of technology and quality expectations. This way, the quality is reliable and customers will be happy to accept it.